Simple maintenance tips can help capture more yield and extend the life of your corn head.
“Many producers focus on the combine when it comes to fall service,” says Iowa farmer and Dragotec USA president Denny Bollig, “but there’s plenty of reason to understand the importance of maintaining the corn head, too.
“More than 60% of the yield lost during harvest occurs at the corn head,”* he says. “Proper maintenance of the corn head not only can extend its life but help reduce harvest loss.”
He notes that along with preharvest maintenance recommended for the corn head brand, producers should be routinely inspecting key components, including deck plates, knife rollers and gearboxes through the harvest season.
“And think twice about replacing worn parts such as blades, choppers and gathering chains with cheap off brand parts — those can cost you more than you think,” Bollig says.
Harvest conditions
Bollig points out that harvest conditions have a great impact on maintenance needs — from the previous year as well as the season ahead.
“Downed corn, for example, forces placement of the head closer to the ground, bringing in more dirt, debris and stones,” he says. “This means your maintenance just went up — including everything from lubrication to cleaning — to keep your corn head running at peak performance.”
Those conditions, Bollig says, suggest the importance of good header height control, such as Headsight® Terrahawk radar height control, a noncontact height sensor.
“There was a lot of downed corn last year, especially in Iowa following the derecho high-wind event,” he says. “Those producers, in particular, should be looking for wear and damage, if they haven’t already.”
Deck plate calibration
“Deck plate alignment is critical to getting more yield acre after acre,” he says. “Over time, debris, linkage wear and field obstacles can cause hydraulic deck plate gaps to deviate among row units from the original factory-set calibration.”
He notes that university research** has shown that as little as one-eighth of an inch deck plate misalignment between rows can result in a 1 in 4 bushel per acre loss.
“We now know that stalk thickness variability is significant in today’s corn hybrids — especially in higher-yielding corn,” Bollig says. “It’s greater than what hydraulic deck plates and today’s wider corn heads can compensate. Nonetheless, it’s important to check gap consistency between deck plates at least once a year — and during the season if possible — to ensure there are no major discrepancies among row units,” Bollig says. “Failure to do so could lead to unnecessary yield loss.”
He points out that Drago corn heads with automatic self adjusting deck plates don’t require calibration and provide added self-cleaning action from constant movement.
Inspect knife rollers
Harvesting high-yielding corn requires consistent feeding action at the knife rollers. Although this may seem like an obvious maintenance checkpoint, Bollig says farmers often overlook knife roller wear and spacing, which can cost yield.
“Worn knife rollers can create stalk slippage during pull-down and require higher speeds to process plant material,” says Bollig. “And a consequence of a higher knife roller speed is an increase in yield loss via butt shelling and ear loss.”
He adds that most knife roller designs have a short window to fully process stalks. Inefficient stalk processing means stalks can bunch up. “Farmers naturally compensate for this by increasing roller speed, but in doing so, create additional wear in a concentrated area at the front of knife rollers.”
Overlooking knife roller maintenance — or having to change knife rollers during the harvest season — can add significant time and cost on top of yield reductions. It’s important to be proactive and not try and press your luck going into harvest.
Evaluate drive system components
Other maintenance trouble spots include corn head drive system components. In addition to examining the drive system for signs of wear, producers should also check both the level and condition of grease or gear oil in each row unit gearbox.
“Gearboxes are at the heart of any corn head and their wear can be a great indicator of its longevity,” says Bollig. “Producers might consider replacing their corn head when major drive components, including row unit gearboxes, begin to fail or when there is excessive backlash movement of rotating shafts and sprockets.”
Replacing parts
Inevitably, as chains, sprockets and gears wear, drive system components lose efficiency. Producers must use their discretion when weighing the cost of repairs versus replacement.
“When making a decision about part replacements, ask yourself, ‘What is it going to cost me?’ without just thinking about the cost of the part itself,” Bollig advises. “Consider the job it will do and if it will last the season.”
It’s also important to consider the age and expected life of your corn head.
“Metalurgical tests and studies on Drago knife roller blades and gathering chains, for example, show our OEM blades perform three times longer than off-brand blades, and that our gathering chains perform two times longer than offbrand chains,” Bollig says.
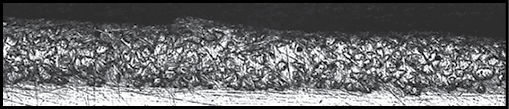
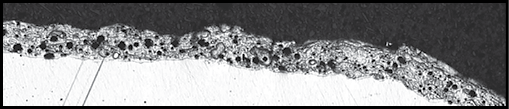
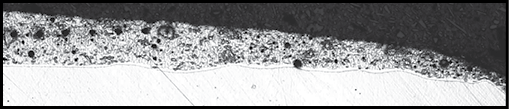
“So while the cost of an off-brand part may be cheaper initially, the cost of added purchases and labor can make them significantly more expensive over time.”
Bollig notes that cheaper replacement parts can unexpectedly impact related components, too.
“Lower-quality gathering chains, having less or inconsistent application of chrome on pins than OEM Drago chains for example, don’t run as smoothly, create more friction and cause undue wear on the sprockets they run on,” Bollig says. “It isn’t just the chains you’ll be replacing.”
Sprocket wear with Drago gathering chains
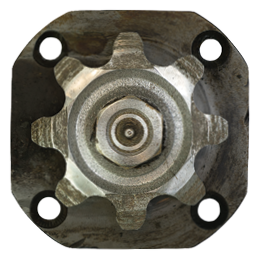
Sprocket wear with off-brand gathering chains
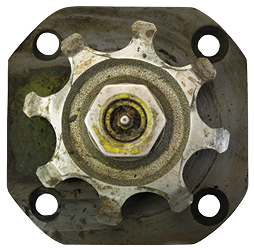
Other maintenance considerations
Referencing the operator’s manual is always a good way for producers to bring themselves back up to speed on the proper maintenance of their corn head. Other routine corn head care procedures include:
- Maintaining normal or severe service lubrication schedules to help avoid breakdowns.
- Blowing the row units off under the bonnets to keep all parts moving freely.
- Cleaning gathering chain tensioners regularly. Proper tension adds life to chains and sprockets.
“Good management and good maintenance go hand in hand,” says Bollig. “And while factors such as build quality, weather and corn-on-corn practices can also affect the lifespan of a corn head, it won’t last unless properly maintained.”
He notes that more than ever, producers are looking at how corn heads are built for durability when making purchase decisions. “Drago’s design features like spiral-cut bevel gearboxes, chainless drives and longer knife rollers play a role in how a corn head performs and can help extend the life of the head.”
* Iowa State University, Verifying Combine Adjustments During Crop Harvest, Sept. 26, 2019
**Graeme Quick, Iowa State University