Drago corn heads are built in the most advanced facility of its kind.
If there’s a common goal among North American farmers and those around the world, it’s getting the most yield — the most return — from every field of corn they grow. And increasingly, more producers are achieving that goal by using Drago corn heads, from Olimac, to harvest it.
Global demand for this exceptional yield-saving and durable corn head has grown exponentially.
Based in Margarita, Italy, Olimac is a recognized brand in the corn growing regions of Europe, Asia and Australia, as well as the U.S. The company has become one of the world’s premier corn head manufacturers.
Demand for Olimac corn heads has steadily grown since 1954, when it introduced the world’s first “integral head” that could both pick and shell corn. With its ongoing yield-saving innovations and reputation for durability, production capacity has steadily grown to match demand.
The most recent plant expansion in 2023 more than doubled production from an expansion just 10 years earlier.
Advanced robotic manufacturing
The plant, in which Drago corn heads are built, is the most advanced and automated manufacturing facility of its kind, using the latest technologies, processes and tools under the supervision of highly skilled engineers and technicians.
The result is the world’s most efficient corn head for minimizing yield loss at harvest.
Along with harvest efficiency, Drago builds for durability. Corn heads today must work through tougher plants at higher populations across more acres than ever before — subjecting equipment to more wear and potential breakdown.
“That’s why ‘good’ just isn’t ‘good enough’ anymore. You have to have an exceptional corn head,” says Denny Bollig, Fenton, Iowa, farmer and Dragotec USA President. “And how do you build for that? You’ve got to have a great factory with unique, precision manufacturing processes and a tremendous amount of robotic equipment to ensure every corn head comes out with the durability and quality today’s farmers need.”
It starts with engineering
The Olimac factory is unique in how every step in the process — from design to final assembly and quality control — happens under the same roof.* That starts with the engineering department or “brain center” where corn heads are designed and the manufacturing processes are monitored and controlled. Because the engineers work in the same facility where the corn heads are assembled, added efficiency is created from the start.
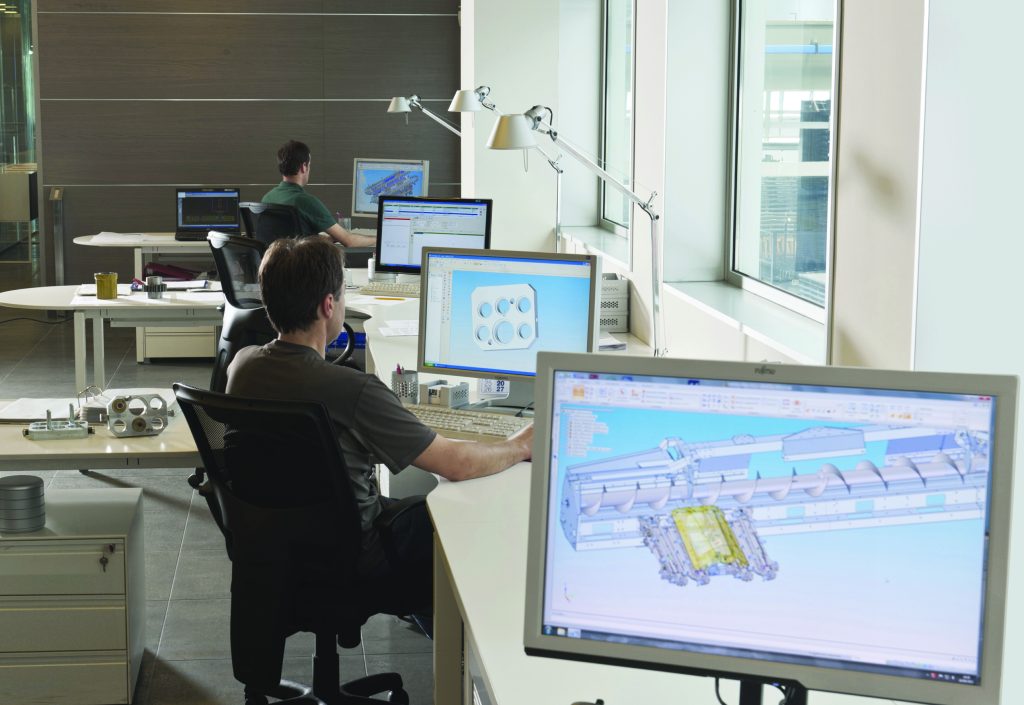
“When a product is designed by the same people, instead of trading it off to another department like that of other manufacturers, the engineer follows that design down to the floor of the factory, works through production, assembly and actually follows it into the field for testing,” Bollig says. “They are extremely efficient.”
Precision machining
Once engineers have passed along designs to the manufacturing floor, quality control is a key part of the first steps in production. Take Olimac’s machining and gear manufacturing, for example. The robotic milling that produces Drago’s spiral-cuts gears, for example, is precise down to the level of a micron, one of the smallest units of measure in manufacturing.
“Olimac has a great saying along the lines of ‘If you want to control quality, you’ve got to control the individual pieces.’” Bollig says. “They have 32 robotic milling machines that do just that for them. Milling down to within half a micron is very unique in farm equipment manufacturing.”
Built to last
That kind of attention to every component leads to a more durable corn head. And durability is extremely important to corn farmers today facing challenging corn market conditions that have them looking for ways to trim costs and maximize revenue.
Each component is engineered, manufactured and tested according to strict specifications beyond industry standards for each process. Because of the precision in these processes, the resulting corn head lasts longer and helps the farmer get a higher return on their investment.
“Olimac has its own quality control lab where they test all gears and parts and make any corrections necessary. It’s extremely precise,” Bollig says of the company’s quality testing. “The precision and attention that goes into this part of the process is a big reason why these corn heads are so durable.”
Personal attention & quality control
Though technology plays a big role in how Drago corn heads are manufactured, the quality testing and control steps in the process depend greatly on the dedication of those building them.
“Olimac’s quality testing and control engineers bring the parts into an actual lab where computers can precisely measure and look for deviation in tolerances in the machining and manufacturing process,” Bollig says. “When that process is done, the inspector actually puts his or her mark on it, making Olimac stand alone in employee accountability and overall quality control.”
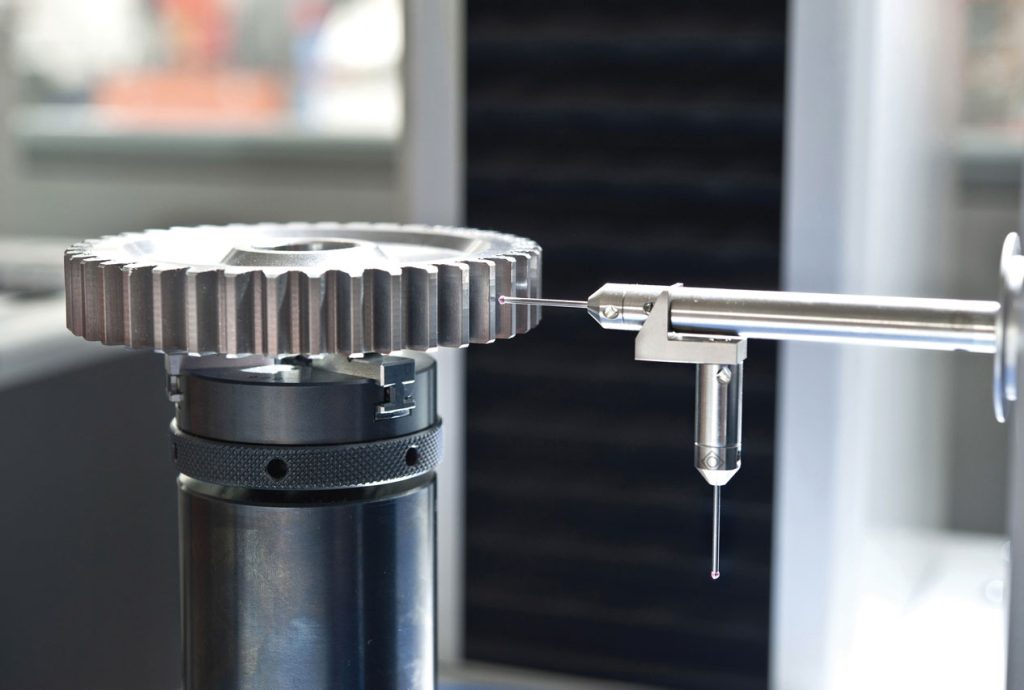
Olimac’s process for quality testing verifies that 100% of the components on the corn head are “to spec” before assembly. In contrast, other brands require an inspection of 10% to achieve ISO 9000 international quality standards.
Family accountability
Drago corn heads are a product of the guidance and leadership of a family who has been devoted to building only corn heads for six decades. With that family involvement comes accountability and attention to every step in the process.
“The Olimac family is in its fourth generation of working together to build corn heads and, more importantly, pass along critical knowledge of harvesting and engineering from one generation to the next,” says Bollig, whose own family is involved in Dragotec USA. “That approach, along with the high technology used in the process, is why Drago corn heads offer tremendous productivity to the corn farmer.”
For more information on Olimac’s dedication to quality and performance, check out the factory video that highlights the precision manufacturing of the Olimac manufacturing facility.
*Zinc is applied to gathering chains outside the Olimac facility.